Introduction
When planning for inventory, a company’s goal is to have the right amount of stock on hand to meet customer demand while minimizing costs and maximizing profits. Inventory management is a critical aspect of any business, as it directly impacts customer satisfaction, cash flow, and overall profitability. Effective inventory planning involves forecasting demand, setting appropriate stock levels, and implementing efficient replenishment strategies.
Forecasting demand is a crucial step in inventory planning. By analyzing historical sales data, market trends, and customer behavior, companies can predict future demand and adjust their inventory levels accordingly. Accurate demand forecasting helps businesses avoid stockouts, where products are out of stock, and overstock situations, where excess inventory ties up valuable capital and storage space.
Setting appropriate stock levels is another key aspect of inventory planning. Companies need to strike a balance between having enough stock to meet customer demand and avoiding excessive inventory. This involves determining the optimal reorder point, which is the inventory level at which new stock should be ordered, and the economic order quantity, which is the ideal batch size for replenishment. By setting these parameters correctly, businesses can minimize stockouts and reduce carrying costs associated with excess inventory.
Implementing efficient replenishment strategies is essential for effective inventory management. This involves establishing relationships with reliable suppliers, negotiating favorable terms, and implementing systems to track and manage inventory levels in real-time. Just-in-time (JIT) inventory management is a popular strategy that aims to minimize inventory holding costs by ordering and receiving goods just in time for production or customer delivery. By streamlining the replenishment process, companies can reduce lead times, improve cash flow, and enhance overall operational efficiency.
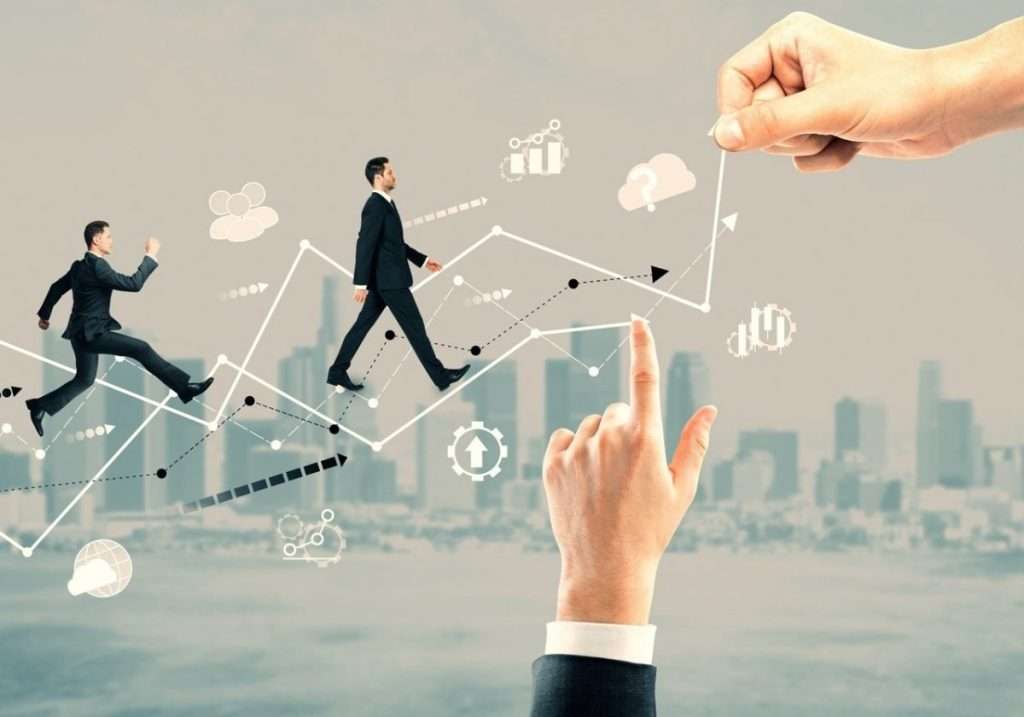
What is a company’s goal when planning for inventory?
A company’s goal when planning for inventory is to strike a balance between meeting customer demand and minimizing costs. Inventory planning involves determining the optimal levels of inventory to have on hand at any given time, taking into account factors such as customer demand, lead times, and production capabilities.
One of the primary goals of inventory planning is to ensure that a company has enough inventory to meet customer demand. This involves forecasting customer demand based on historical data, market trends, and other relevant factors. By accurately predicting demand, a company can ensure that it has enough inventory on hand to fulfill customer orders in a timely manner.
However, it is also important for a company to avoid overstocking inventory, as this can tie up valuable resources and increase carrying costs. Carrying costs include expenses such as storage, insurance, and obsolescence, which can significantly impact a company’s profitability. Therefore, a company’s goal when planning for inventory is to find the right balance between having enough inventory to meet customer demand and minimizing carrying costs.
Another goal of inventory planning is to minimize stockouts and backorders. Stockouts occur when a company runs out of a particular product, while backorders occur when a customer places an order for a product that is currently out of stock. Both stockouts and backorders can result in lost sales and dissatisfied customers. Therefore, a company’s goal when planning for inventory is to ensure that it has enough inventory on hand to avoid stockouts and backorders.
However, carrying excess inventory can also be costly, as it ties up capital and increases carrying costs. Therefore, a company must carefully balance the costs of carrying excess inventory against the costs of stockouts and backorders when planning for inventory.
What is the planning of inventory management?
Inventory management planning refers to the process of determining the optimal levels of inventory that a company should maintain in order to meet customer demand while minimizing costs. It involves forecasting demand, setting inventory targets, and implementing strategies to achieve those targets. Effective inventory management planning is crucial for businesses to ensure smooth operations, minimize stockouts, and avoid excess inventory.
Forecasting demand is a key component of inventory management planning. By analyzing historical sales data, market trends, and customer behavior, businesses can estimate future demand for their products. This helps them determine the appropriate levels of inventory to have on hand to meet customer needs. Accurate demand forecasting is essential to avoid stockouts, which can result in lost sales and dissatisfied customers, as well as excess inventory, which ties up capital and increases carrying costs.
Setting inventory targets is another important aspect of inventory management planning. This involves determining the desired levels of inventory for each product or SKU (stock-keeping unit) based on factors such as lead time, demand variability, and desired service levels. Inventory targets can be set using various methods, such as the economic order quantity (EOQ) model or the reorder point (ROP) model. These targets serve as guidelines for replenishing inventory and help businesses maintain optimal stock levels.
Implementing strategies to achieve inventory targets is the final step in inventory management planning. This involves making decisions on when and how much to order, as well as how to handle excess or slow-moving inventory. Strategies may include just-in-time (JIT) inventory management, where inventory is ordered and received just in time to meet customer demand, or safety stock, which is extra inventory held as a buffer against unexpected fluctuations in demand or supply. By implementing effective strategies, businesses can optimize their inventory levels and improve overall operational efficiency.
Why is inventory planning important?
Inventory planning is a crucial aspect of any business, regardless of its size or industry. It involves determining the optimal level of inventory to have on hand in order to meet customer demand while minimizing costs and maximizing profitability. Effective inventory planning ensures that a company has the right amount of inventory at the right time, preventing stockouts and excess inventory.
One of the main reasons why inventory planning is important is because it helps businesses meet customer demand. By accurately forecasting demand and planning inventory levels accordingly, companies can ensure that they have enough products available to fulfill customer orders in a timely manner. This is particularly important for businesses that operate in industries with seasonal or fluctuating demand patterns. Without proper inventory planning, companies risk losing sales and customers due to stockouts, which can have a negative impact on their reputation and bottom line.
Another reason why inventory planning is important is because it helps businesses manage costs and improve profitability. Holding excess inventory ties up valuable capital and incurs additional costs such as storage, insurance, and obsolescence. On the other hand, stockouts can result in lost sales and the need for expedited shipping, which can be costly. By accurately forecasting demand and planning inventory levels, businesses can optimize their inventory investment and reduce costs associated with carrying excess or insufficient inventory.
Inventory planning also plays a crucial role in supply chain management. It helps businesses maintain a smooth flow of goods from suppliers to customers, ensuring that there are no disruptions or delays in the supply chain. By having the right amount of inventory at the right time, businesses can minimize lead times and improve order fulfillment rates. This not only enhances customer satisfaction but also strengthens relationships with suppliers and reduces the risk of stockouts or excess inventory.
What is the basic concept of inventory planning?
Inventory planning is the process of determining the optimal quantity and timing of inventory to meet customer demand while minimizing costs. It involves forecasting demand, setting inventory levels, and managing the replenishment process. The goal of inventory planning is to ensure that the right products are available in the right quantities at the right time to satisfy customer needs.
One of the basic concepts of inventory planning is demand forecasting. This involves analyzing historical sales data, market trends, and other relevant factors to predict future demand for a product. Accurate demand forecasting is crucial for determining the appropriate inventory levels to maintain. If demand is overestimated, excess inventory may be held, leading to increased carrying costs and potential obsolescence. On the other hand, if demand is underestimated, stockouts may occur, resulting in lost sales and dissatisfied customers.
Another important concept in inventory planning is setting safety stock levels. Safety stock is a buffer inventory that is held to protect against unexpected fluctuations in demand or lead time. It acts as a cushion to ensure that there is enough inventory available to meet customer demand even during periods of high variability. The level of safety stock is determined based on factors such as desired service level, lead time variability, and demand variability.
Inventory turnover is also a key concept in inventory planning. It refers to the number of times inventory is sold or used up in a given period. A high inventory turnover indicates that inventory is being efficiently managed and that products are moving quickly through the supply chain. On the other hand, a low inventory turnover may indicate excess inventory or slow-moving products, which can tie up capital and increase carrying costs.
Effective inventory planning requires a balance between maintaining sufficient inventory to meet customer demand and minimizing the costs associated with holding inventory. This involves considering factors such as lead time, order quantities, carrying costs, and service level targets. By optimizing inventory levels and replenishment processes, businesses can improve customer satisfaction, reduce costs, and enhance overall operational efficiency.
What is the main purpose of inventory management?
Inventory management refers to the process of overseeing and controlling the flow of goods and materials within a company. It involves the management of inventory levels, ordering and replenishing stock, and ensuring that the right products are available at the right time. The main purpose of inventory management is to strike a balance between having enough inventory to meet customer demand and minimizing the costs associated with holding excess inventory.
One of the primary goals of inventory management is to ensure customer satisfaction. By having the right products in stock and readily available, companies can fulfill customer orders in a timely manner. This helps to build customer loyalty and maintain a positive reputation in the market. Additionally, inventory management allows companies to accurately forecast demand and plan production accordingly, reducing the risk of stockouts and backorders.
Another important purpose of inventory management is to optimize cash flow. Inventory ties up a significant amount of capital, and holding excess inventory can lead to increased carrying costs, such as storage, insurance, and obsolescence. By effectively managing inventory levels, companies can minimize these costs and free up cash for other business activities, such as investing in new products or expanding operations.
Inventory management also plays a crucial role in cost control. By closely monitoring inventory levels and implementing efficient ordering and replenishment processes, companies can reduce the risk of overstocking or understocking. Overstocking can result in increased holding costs and potential losses due to product obsolescence, while understocking can lead to missed sales opportunities and dissatisfied customers. By maintaining optimal inventory levels, companies can minimize these costs and maximize profitability.
Furthermore, inventory management helps in streamlining operations and improving efficiency. By implementing inventory management systems and processes, companies can automate various tasks, such as tracking inventory levels, generating purchase orders, and managing stock movements. This reduces the need for manual intervention and minimizes the risk of errors. Additionally, inventory management allows companies to identify and eliminate bottlenecks in the supply chain, improving overall operational efficiency.
What is the primary objective of a company when planning for inventory?
The primary objective of a company when planning for inventory is to strike a balance between meeting customer demand and minimizing costs. Inventory planning involves determining the optimal level of inventory to have on hand at any given time. This is crucial because having too much inventory ties up valuable resources and increases storage costs, while having too little inventory can result in stockouts and lost sales.
By effectively planning their inventory, companies can ensure that they have enough stock to fulfill customer orders in a timely manner, while also avoiding excess inventory that can lead to obsolescence or spoilage. This requires careful analysis of historical sales data, market trends, and demand forecasts. Additionally, companies must consider factors such as lead times, production capacity, and supplier reliability to ensure a smooth and efficient supply chain.
What strategies can a company employ to achieve its inventory goals?
When it comes to achieving inventory goals, companies can employ several strategies to ensure efficient management of their inventory. One strategy is implementing a Just-in-Time (JIT) inventory system. This approach involves keeping inventory levels as low as possible by only ordering and receiving goods when they are needed for production or customer demand. By reducing excess inventory, companies can minimize carrying costs and improve cash flow.
Another strategy is implementing a robust demand forecasting system. By accurately predicting customer demand, companies can optimize their inventory levels and avoid stockouts or overstock situations. This can be achieved through the use of advanced analytics and historical sales data. Additionally, companies can collaborate closely with suppliers and customers to gather insights and align their inventory levels with market demand.
How does effective inventory planning contribute to a company’s overall success?
Effective inventory planning plays a crucial role in a company’s overall success. By ensuring that the right amount of inventory is available at the right time, a company can optimize its operations, reduce costs, and improve customer satisfaction. One of the key benefits of effective inventory planning is improved cash flow management. By accurately forecasting demand and maintaining optimal inventory levels, a company can avoid overstocking or understocking, which can tie up valuable capital or result in lost sales.
Additionally, effective inventory planning enables a company to minimize stockouts and backorders. By having the right products in stock, a company can fulfill customer orders promptly, leading to increased customer satisfaction and loyalty. This, in turn, can result in repeat business and positive word-of-mouth referrals. Moreover, effective inventory planning allows a company to streamline its supply chain and reduce lead times. By having a clear understanding of inventory needs and collaborating closely with suppliers, a company can minimize delays and disruptions, ensuring timely delivery of products to customers.
” “When planning for inventory, a company’s goal is to have an efficient and effective system in place that ensures the right amount of products are available at the right time. This is crucial for meeting customer demand, minimizing costs, and maximizing profits. By carefully analyzing historical data, forecasting future demand, and implementing appropriate inventory management techniques, companies can achieve this goal.
One key aspect of inventory planning is understanding customer demand patterns. By analyzing historical sales data, companies can identify trends and patterns that can help them forecast future demand. This allows them to determine the optimal level of inventory to have on hand at any given time. For example, if sales tend to spike during certain seasons or holidays, the company can plan to have higher inventory levels during those times to meet the increased demand. On the other hand, if sales are consistently low during certain periods, the company can reduce inventory levels to avoid excess stock and associated costs.
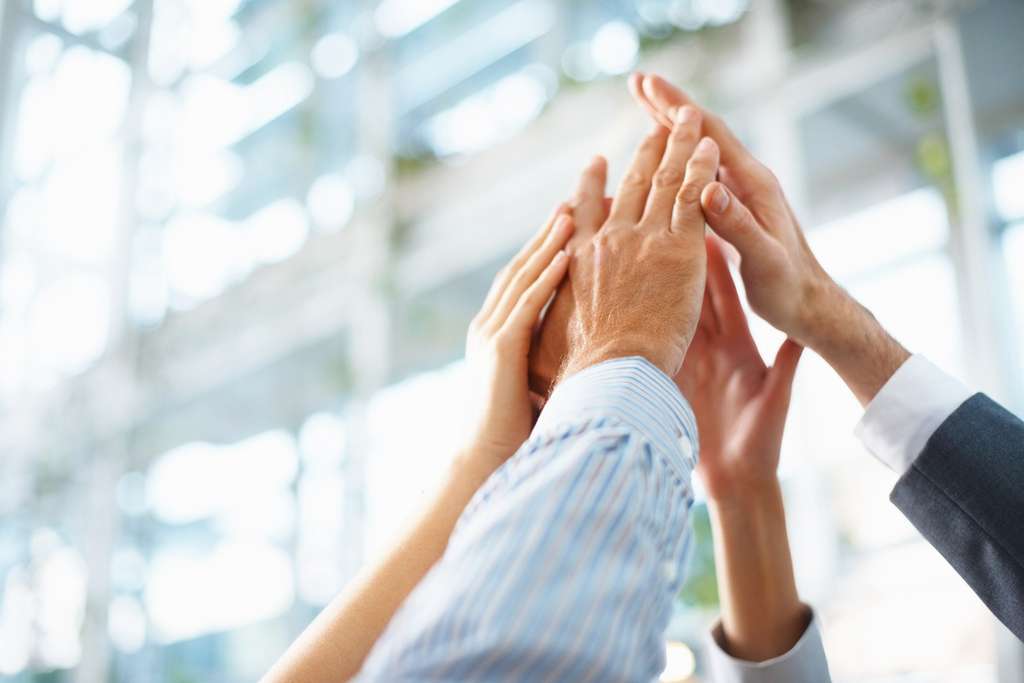
Conclusion
Another important consideration in inventory planning is the lead time for replenishing inventory. Lead time refers to the time it takes for a company to receive new inventory after placing an order. By accurately estimating lead time, companies can ensure they have enough inventory on hand to meet customer demand while minimizing the risk of stockouts. This requires close collaboration with suppliers and accurate tracking of order and delivery times. Companies may also consider implementing safety stock, which is extra inventory held as a buffer to account for unexpected delays or fluctuations in demand.
Effective inventory planning also involves implementing appropriate inventory management techniques. This includes strategies such as just-in-time (JIT) inventory management, which aims to minimize inventory holding costs by receiving inventory just in time for production or customer delivery. JIT can help reduce waste, improve cash flow, and increase overall efficiency. Other techniques include ABC analysis, which categorizes inventory based on its value and importance, and economic order quantity (EOQ) analysis, which determines the optimal order quantity to minimize costs.