Introduction
What Is Cycle Time In Operations Management: Cycle time is a fundamental concept in the field of operations management, serving as a critical metric that plays a pivotal role in optimizing processes and improving efficiency within organizations. It represents the amount of time it takes to complete a specific task, operation, or process from start to finish. In essence, cycle time provides a clear measurement of the speed and effectiveness of a particular operation or workflow, making it an invaluable tool for businesses seeking.Â
To streamline their operations, enhance productivity, and meet customer demands more effectively. Understanding and managing cycle time is essential for achieving operational excellence and maintaining a competitive edge in today’s fast-paced business environment. Will delve deeper into the concept of cycle time, exploring its significance, measurement, and its vital role in operations management.
By carefully analyzing and optimizing cycle times, organizations can identify bottlenecks, reduce unnecessary delays, and enhance resource allocation. This, in turn, helps in meeting customer time management expectations, improving product quality, and reducing operational costs. Whether it’s streamlining production lines, shortening service delivery times, or managing project schedules, cycle time management is a cornerstone of operations excellence.
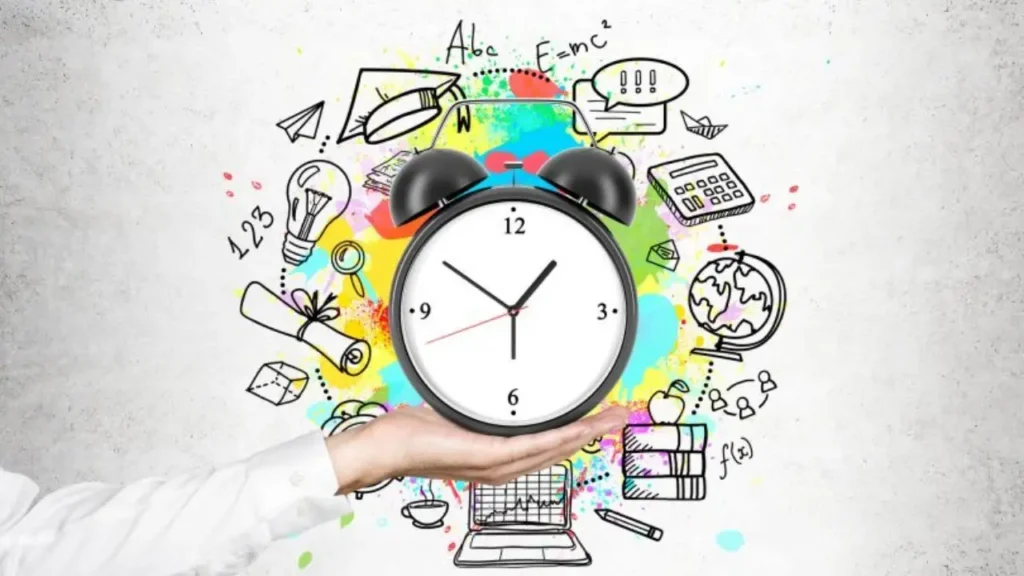
What is the cycle time of operations?
Cycle time is the actual time spent working on producing an item or providing a service, measured from the start of the first task to the end of the last task. Cycle time includes both value-added time as well as non-value-added time.
Cycle time is a fundamental metric in operations management that quantifies the time it takes to complete a specific task, operation, or process from start to finish. It serves as a key performance indicator (KPI) for assessing the efficiency and effectiveness of various operations within an organization. Cycle time measurement can be applied to a wide range of scenarios, including manufacturing, service delivery, project management, and more.
Process Efficiency: Cycle time reveals how efficiently a process is operating. By identifying bottlenecks and delays, organizations can make informed decisions to streamline operations and reduce waste.
Resource Allocation: It helps in allocating resources effectively. Knowing how much time is required for different tasks allows organizations to allocate labor, equipment, and other resources optimally.
Quality Improvement: Shorter cycle times often lead to better product or service quality. Faster processes are less prone to errors and deviations, resulting in improved customer satisfaction.
Customer Satisfaction: In today’s fast-paced world, customers expect prompt service and delivery. Meeting or exceeding customer expectations for quick turnaround times is essential for retaining and attracting clients.
What is cycle time and process time?
Process time is focused on specific tasks or development stages. It’s a more granular approach to operational analysis. In contrast, cycle time is all about the big picture. It’s the sum of all the process time added together plus any extra waiting or delays, like transportation or an approval process.
Scope: The primary difference between cycle time and process time lies in their scope. Cycle time encompasses the entire duration of a process, including both value-added and non-value-added activities, while process time isolates and measures only the value-added portion.
Efficiency Assessment: Cycle time is used to evaluate the overall efficiency of a process, including areas where improvements can be made, such as reducing wait times and optimizing workflows. Process time, on the other hand, focuses specifically on the efficiency of the value-adding steps within the process.
Resource Allocation: Understanding both cycle time and process time is crucial for resource allocation. Organizations can use process time to determine how long specific tasks take, helping with staffing decisions and resource allocation. Cycle time, in contrast, guides decisions on process redesign and streamlining.
Manufacturing: In manufacturing, cycle time is vital for optimizing production lines, while process time is used to fine-tune individual manufacturing steps to increase efficiency.
Healthcare: In healthcare, process time helps improve patient care by reducing the time it takes for medical procedures, while cycle time is used to assess the overall patient journey.
What is an example of cycle time?
For example, if a machine has a cycle time of 20 seconds, plus a combined load and unload time of 30 seconds, and a changeover time of 30 seconds divided by a minimum batch size of 30, the Effective Machine Cycle Time is 20+30+(30/30) or 1 = 51 seconds.
Automobile Production Line: In automobile manufacturing, cycle time is a key metric. For instance, consider the assembly of car doors. The cycle time here would represent the time it takes for a worker or a robotic arm to install a door on a vehicle. By minimizing this cycle time, the production line can increase output, reduce labor costs, and meet customer demands for faster delivery.
Bottling Plant: In a bottling plant, cycle time is crucial for filling and capping bottles. Shortening the cycle time for these processes can result in higher production volumes, reduced energy consumption, and a more streamlined supply chain.
Emergency Room (ER) Triage: In a hospital ER, cycle time is a matter of life and death. The cycle time here represents the time from a patient’s arrival to their initial assessment by a healthcare provider. Reducing this cycle time ensures that critically ill patients receive prompt attention, improving patient outcomes.
Laboratory Testing: In a medical laboratory, cycle time is essential for diagnostic testing. Shortening the cycle time for processing blood samples or pathology tests allows healthcare providers to make faster treatment decisions, potentially saving lives.
Why do we calculate cycle time?
Benefits of calculating cycle time
Identifies areas of improvement: Cycle times can show where a business can optimize its operations to improve sales and reduce the time it takes to produce a product. Cycle times can help pinpoint exactly what may be causing production to slow down.
One of the primary reasons for calculating cycle time is to assess the performance of a process or operation. By measuring how long it takes to complete a task or produce a product, organizations gain a clear understanding of their operational efficiency. This evaluation helps identify areas where improvements are needed and provides a baseline for future performance comparisons.
Cycle time acts as a diagnostic tool for process optimization. When organizations break down the elements contributing to cycle time, they can pinpoint bottlenecks, delays, or inefficiencies within their operations. Armed with this information, they can make informed decisions to streamline processes, eliminate waste, and enhance productivity.
Efficient resource allocation is another critical aspect of calculating cycle time. By knowing how long specific tasks or operations take, organizations can allocate resources more effectively. This includes assigning the right number of personnel, equipment, and materials to ensure optimal productivity without overburdening resources.
Cycle time is closely linked to product and service quality. Shorter cycle times often lead to better quality outcomes because faster processes are less susceptible to errors and deviations. By reducing cycle times, organizations can improve quality, resulting in higher customer satisfaction and fewer defects.
What are the factors affecting cycle time?
Factors such as capacity, labor, manufacturing congestion, inventory, quality of product, and schedule and management affect manufacturing cycle time.
The skill and experience of the workforce involved in a process play a crucial role in determining cycle time. Highly skilled and experienced employees are typically more efficient and can complete tasks faster. Conversely, a lack of expertise or training can lead to longer cycle times.
The availability and efficiency of equipment and technology can significantly impact cycle time. Outdated or malfunctioning equipment can lead to delays, while modern technology and automation can expedite processes, reducing cycle time.
Workload and resource availability affect cycle time in two ways. A high workload or resource constraints can lead to longer cycle times as employees juggle multiple tasks or wait for resources to become available. Conversely, excess capacity can result in shorter cycle times.
Bottlenecks occur when a specific step or resource in a process slows down the entire operation. Identifying and addressing bottlenecks is crucial for reducing cycle time. This may involve reallocating resources, redesigning processes, or investing in additional capacity.
What is cycle time also known as?
Takt Time is a measure of the amount of time between the completion of one unit and the beginning of the next. Cycle time refers to the average time taken to complete a single unit. The Lead Time refers to the length of time it takes from the date of receipt of an order to the date of delivery. Learn for free!
“Process time” is perhaps one of the most frequently used synonyms for cycle time. It refers to the duration required to complete the value-added activities within a process. Process time excludes non-value-added elements, such as waiting or idle time, focusing solely on the time spent actively working on a task or operation.
Lead time is another closely related term that is sometimes used interchangeably with cycle time. However, there is a subtle difference. Lead time encompasses the entire duration from the initiation of a process, including any wait or delay time, to its completion. In contrast, cycle time typically excludes non-value-added elements.
“Turnaround time” is frequently used in service-related industries, such as customer support or help desks. It signifies the time it takes to address and resolve customer inquiries or issues. This term emphasizes the importance of providing timely responses and solutions to customers.
In the context of service-level agreements (SLAs), especially in IT and customer service, cycle time may be referred to as the “SLA response time” or “SLA resolution time.” These terms emphasize the commitment to meeting specific timeframes for addressing customer requests or incidents.
In manufacturing, “manufacturing cycle time” specifically refers to the time it takes to produce a single unit or item. This term is commonly used when assessing the efficiency of production lines and manufacturing processes.
What is the advantage of cycle time?
Cycle time is important because it reflects how quickly and efficiently your team can deliver value to your customers. A low cycle time means that your team can respond faster to changing requirements, feedback, and market conditions, and that your customers can enjoy the benefits of your product sooner.
One of the primary advantages of cycle time measurement is the insight it provides into process efficiency. It allows organizations to identify bottlenecks, delays, or redundancies within processes. By addressing these inefficiencies, businesses can streamline operations, reduce waste, and optimize resource allocation, ultimately leading to improved efficiency.
In manufacturing and product development, shorter cycle times result in faster product development and delivery to the market. This agility allows organizations to respond quickly to changing customer demands and market trends, gaining a competitive edge.
Cycle time directly impacts customer satisfaction. Customers today expect faster service and delivery. By reducing cycle times, organizations can meet or exceed these expectations, leading to higher customer satisfaction and loyalty.
Understanding cycle time helps organizations allocate resources more effectively. Whether it’s assigning the right number of employees to a task, optimizing machine usage in manufacturing, or managing project schedules, efficient resource allocation is essential for cost control and improved productivity.
Cycle time measurement is a cornerstone of continuous improvement efforts. By regularly assessing and analyzing cycle times, organizations can identify trends, evaluate the effectiveness of improvement initiatives, and drive a culture of continuous improvement throughout the organization.
Why reduce cycle time?
Cycle time is one of the primary speed measures — and speed is good. Reducing cycle time leads to: Faster learning — The quicker we ship, the faster we can evaluate outcomes. Higher flexibility — Low cycle time allows us to react faster and change the course of direction more easily.
Perhaps the most apparent reason to reduce cycle time is the immediate improvement in operational efficiency. Shorter cycle times indicate that processes are running more smoothly, with fewer delays and bottlenecks. This efficiency leads to higher productivity, reduced resource waste, and improved overall performance.
Reducing cycle time enables organizations to respond more swiftly to changing customer demands. In today’s fast-paced business environment, customers expect quick turnaround times. By shortening cycle times, businesses can meet or even exceed these expectations, resulting in higher customer satisfaction and loyalty.
Efficiency gains resulting from cycle time reduction often translate into significant cost savings. Faster processes require fewer resources, less energy, and lower overhead costs. Over time, these cost reductions contribute to improved profitability and financial stability.
In highly competitive markets, the ability to deliver products or services faster and more efficiently is a distinct competitive advantage. Organizations that reduce cycle time gain an edge over their rivals by capturing market opportunities, responding to trends, and outperforming competitors in terms of speed and agility.
Reducing cycle time helps organizations optimize resource allocation. Whether it’s labor, machinery, or materials, efficient resource allocation leads to cost control and increased productivity. Organizations can do more with less, which is particularly valuable in resource-constrained environments.
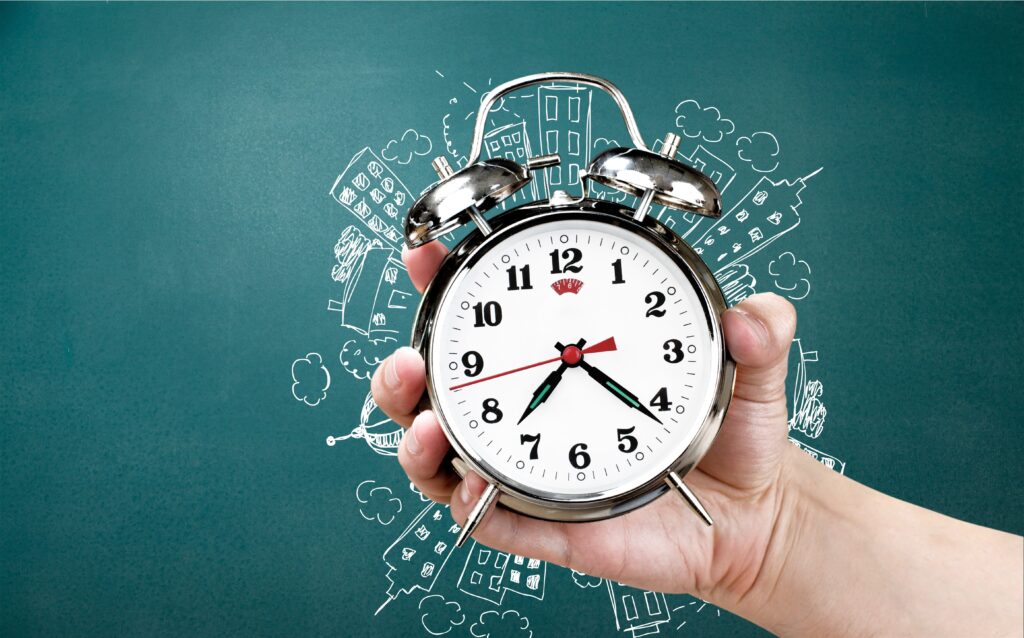
Conclusion
The significance of cycle time extends beyond its practical applications. It serves as a catalyst for continuous improvement and a driver of innovation within organizations. When teams and individuals within an organization focus on reducing cycle times, they often uncover innovative solutions, creative problem-solving, and novel approaches to enhance productivity and quality. This pursuit of efficiency can foster a culture of continuous improvement, where employees are encouraged to identify and eliminate waste, leading to a more agile and adaptive organization.
Cycle time management also plays a crucial role in skill set meeting customer expectations and demands, a cornerstone of business success. In an era where customers expect faster delivery, responsiveness, and high-quality products and services, organizations that excel in managing cycle times gain a significant competitive advantage. This customer-centric approach not only retains existing customers but also attracts new ones, contributing to sustainable growth and profitability.
In sum, cycle time in operations management is more than a mere metric; it’s a strategic tool that empowers organizations to optimize processes, drive innovation, and meet customer expectations. As businesses continue to evolve in a dynamic global landscape, mastering cycle time remains a critical component of achieving operational excellence and long-term success.